
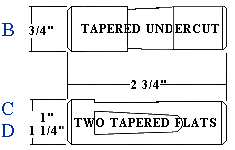
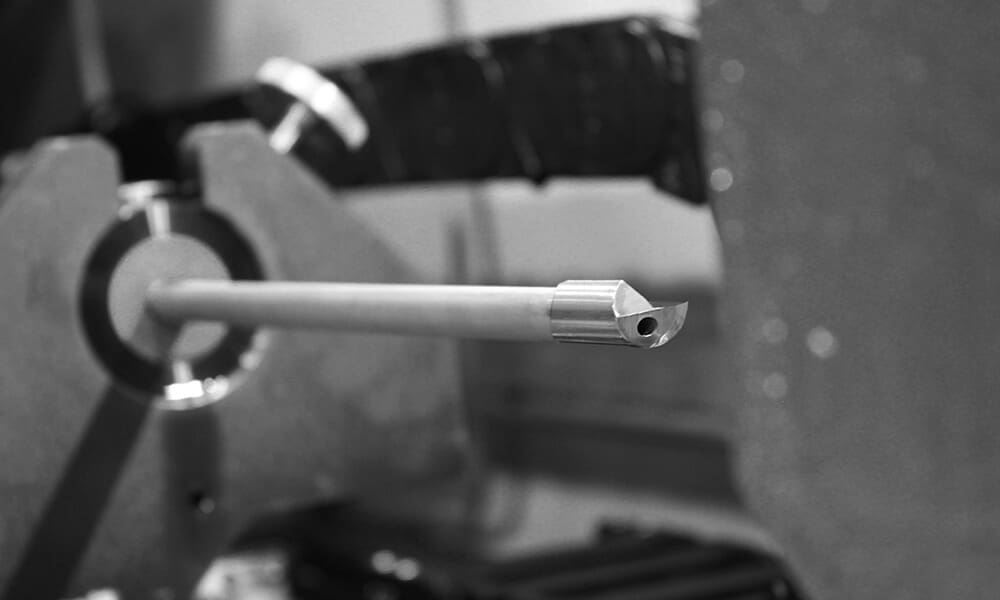
Doubling the hole diameter from 1 to 2" equates to four times more area, and four times more material to evacuate out of the hole. The resulting area amounts to 0.79 in3 (12.95 cm3) for the 1" hole versus 1.77 in3 (29.01 cm3) for the 1.5" hole, a 100 percent increase. Consider the difference between a 1" (25.4 mm) diameter hole and a 1.5" (38.1 mm) diameter one-a 50 percent increase in diameter. A 0.040" (1.016-mm) diameter hole, for example, might require coolant pressure as high as 3,000 psi.īecause there is an exponential factor involved, when hole diameter increases slightly, area/metal removal increases significantly. Conversely, flow rates for small-diameter deep holes may need to be only 2 gpm but with much higher pressure levels. When using larger gundrills or BTA tooling, for instance, the required coolant flow can range from 50 gpm to upwards of 75 to 350 gpm for hole diameters as big as 10 to 12" (25.4 to 30.5 cm). However, much higher volumes are needed to evacuate chips in drilling operations as holes become larger in diameter and/or deeper. Typical flood coolant systems, for example, provide about 10-gpm to around 40-gpm flow rates, depending on the system. Shops often have no idea how much coolant their system delivers or should be delivering. While most shops stop with these systems, even for demanding drilling applications, filtration and coolant alone fail to address one of the most important variables in high-pressure coolant use, which is flow rate. When considering 1,000-plus psi systems, 20- to 50-level filtration is needed to keep pumps from failing, and in most instances, high-pressure coolant systems will require a chiller to regulate coolant temperature.

However, as coolant pressures increase, so too does the need for proper filtration and temperature control. Deep hole drilling machine OEMs such as UNISIG will engineer coolant systems, such as this one, as well as controls into the design of a machine to ensure integration as well as performance consistency.
Gun drill parameters driver#
Drilling applications, mainly those using twist drills, were a main driver of the development of high-pressure coolant systems, in particular deep hole drilling applications where depth-to-diameter ratios are typically 10:1 and beyond. Then the advent of high-pressure coolant systems operating at around 1,000-plus psi changed the coolant technology landscape with especially effective tool cooling as well as efficient chip evacuation for most conventional machining operations. The result is a system with the adjustability necessary to ensure there is never more pressure in the coolant system than is required for effective chip evacuation and precise drilling.įor many years, the most advanced coolant delivery system beyond flood types were through-spindle/through-tool coolant systems. This requires programmable, infinitely variable flow-based control capability integrated into the deep hole drilling machine itself. Careful management of coolant pressure, filtration, temperature and flow rate is key to optimizing deep hole drilling processes. Coolant is so critical to the deep hole drilling process that today’s state-of-the-art deep hole drilling systems control it much the same as they would a machine’s spindle or axes.
